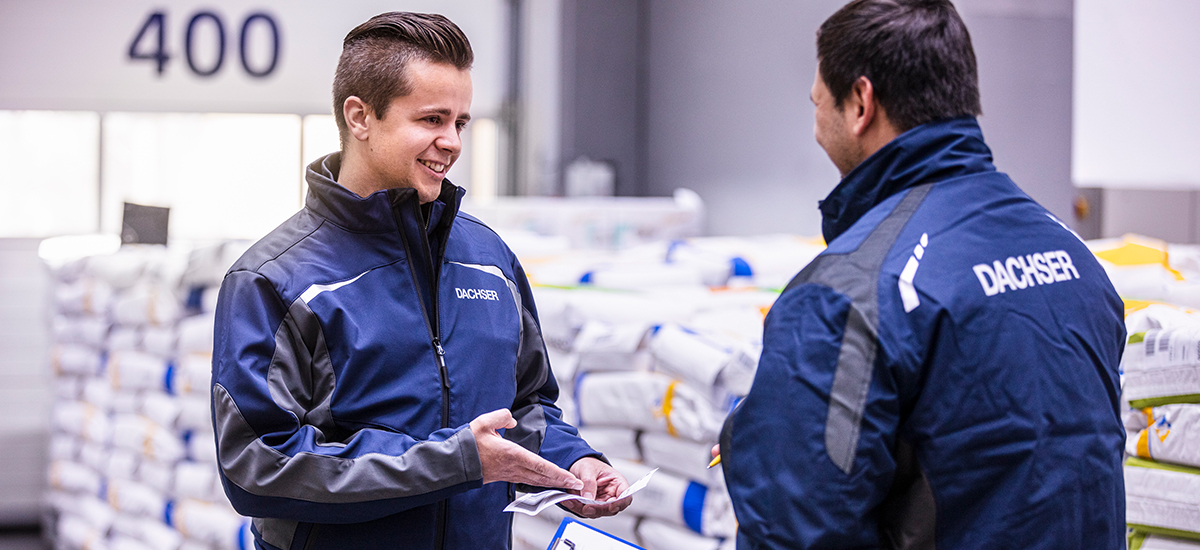
Passion for food
Convince yourself of the high logistical quality of the partners of the European Food Network. For temperature-controlled transports of your foodstuffs, from ultra-fresh to ambient, we offer you not only a sophisticated quality management system, but also highly qualified employees, end-to-end IT-controlled processes and over 200 warehouse locations certified for the storage of foodstuffs within Europe. We deliver high-quality products such as meat, sausage and dairy products, wine and spirits, baked goods and confectionery, convenience items as well as delicatessen or nutrients efficiently and safely to every corner of Europe at scheduled times. Every year, we deliver more than 450,000 consignments of foodstuffs to retail companies, catering businesses, bulk consumer services and processing companies in the food industry via the European Food Network using state-of-the-art vehicles. This is a real sign of trust from our clients, who use the high quality of our services and our sustainability-oriented logistics with our closely timed scheduled services for their transports every day.
- Standardised logistics services for your pan-European food transports
To ensure that food is delivered reliably to its destination as required by the customer, the partners of the European Food Network have implemented uniform standards for the transport of food on the network side. With a focus on food safety and cost efficiency, binding standards include the following
- Logistical processes and procedures that are controlled and monitored due to the continuous coupling of the IT systems
- Europe-wide consistent temperature controls and hygiene measures
- Increasing efficiency around the supply chain
- Uniform service profiles with consistently high quality (vivengo)
In addition, due to the close connection of the partners, you can use fixed-cycle transports for your shipments, which enables a transparent and plannable handling of your shipments across Europe. Not only the network partners can track the current location of their customers' goods in Europe, even for individual pallets. You as a customer can also call up the consignment status online and receive a digitalised delivery receipt after delivery. The flow of information accompanying the goods via Tracking & Tracing is realised throughout Europe. With our control measures, which are based on the requirements of IFS Logistics and include the inspections of logistics activities related to food, such as transport, storage, distribution, loading and unloading, we check within the network whether we comply with the defined standards within the supply chain.
- We ensure the security of your general cargo shipments
The quality assurance of your food transports is close to our hearts. To ensure that you are on the safe side, we have established a comprehensive system of quality assurance and quality management. Fixed performance criteria with target values and quality indicators are the starting point for our sophisticated quality control. By means of numerous evaluations and analyses, we check, among other things, the quality of delivery, the transit times of the consignments, possible damage to the goods or obstacles to delivery at the recipient's premises, and we continuously monitor the cold chain. Based on the findings, we also drive a continuous improvement process in cooperation with the customer in the sense of learning companies. It goes without saying that the HACCP principles are mandatory for all partners and their operational divisions within the network, such as
- identification of hazards
- determination of the critical steering points
- determination of limit values
- monitoring of the critical control points
- determination of corrective measures
- establishment of procedures to verify the HACCP concept
- documentation and records of, for example, temperature lists, time information, instructions on staff and operational hygiene, and cleaning schedules
Likewise, the partners of the European Food Network have committed themselves to European and national quality standards, including: DIN EN ISO 9001 - IFS Logistics - ISO 22000 - BRC - BIO certification (VO (EG) Nr. 834/2007) - ISO 14001.
- The temperature must be right
We must do everything in our power to prevent the destruction of food. This is a claim that we are committed to. In summer and winter, the network partners keep the ambient temperature of the goods in their vehicles and at the handling points constant. Throughout the entire network, we ensure that the temperature is maintained in the range of +2 to +7 degrees Celsius and even offer temperature maintenance in the range of +2 to +4 degrees Celsius on some routes. To ensure this, we take many other temperature-stabilising measures in addition to the exclusive use of certified refrigerated vehicles, such as
- sufficiently long pre-cooling of the vehicles in summer
- predictive loading for optimum air circulation in the vehicle
- loading and unloading via insulated dock levellers
- rapid handover to the recipient - with cold curtain and short door opening times
- the application of trained behaviour for "Good Hygiene Practice" with HAACP-based procedural instructions and process descriptions
- the use of personnel specially trained for the storage and transport of temperature-controlled goods
- the recording of the air temperature inside the vehicles
- ensuring the traceability of the transported food
- Keeping an eye on the right packaging and professional loading
Essential criteria for us to transport your foodstuffs within Europe undamaged are, above all, correctly executed packaging and loading that is safe for operation and transport.
As a shipper, you are responsible for packing food on pallets in a way that is suitable for transport. "Proper" means above all "securely packed" as well as making full use of the given space on the pallet and making sure that overhangs are consistently avoided. In order to prevent possible packaging errors in advance, we offer our customers comprehensive support. On request, our packaging professionals provide assistance in all relevant areas of safe packaging. The benefits are high because correct packaging saves money and time in several respects. The space on a pallet is used more efficiently and damage and unnecessary repackaging are prevented.
After the packaging comes the loading. Professional loading is a basic requirement for protection against dynamic loads during transport by truck. For example, emergency or hazard braking as well as sudden evasive movements should not lead to damage. Particularly general cargo consignments that are distributed throughout Europe sometimes have to be handled several times, are subject to significantly higher loads and are thus more likely to be exposed to possible damage.
In order to achieve a uniform, high quality standard also in loss prevention, the European Food Network partner DACHSER, for example, has set up an extensive programme for loading training. In the branches, coaches are trained in the areas of load securing, damage and loss prevention. These training courses are not only about safe loading, but also about damage prevention and the optimal utilisation of the means of transport. More than 100 coaches have already been trained, who in turn conduct the training sessions for the employees involved. The programme was launched in Germany and is being rolled out successively throughout Europe.
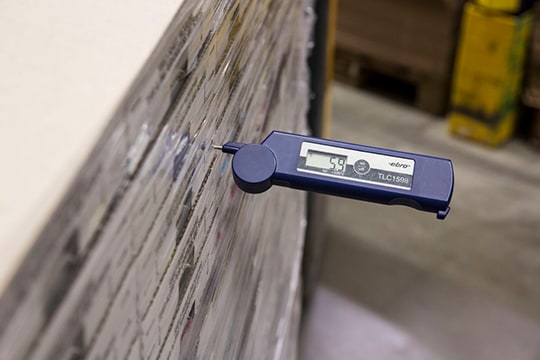
The cornerstones of our quality promise
Digitalisation: The high-performance infrastructure of the physical network and IT with standardised processes ensures smooth and efficient handling of cross-border shipments.
Intelligent traffic routing: As a learning organisation, we permanently adapt traffic routing, forms of handling and capacities to the needs of our customers, taking into account optimised costs. In doing so, we integrate new technological developments to permanently optimise the supply chain.
Highly specialised staff for food transport: We, the partners of the European Food Network, invest permanently in the training and further education of our employees in order to maintain and improve the quality defined via standards at a consistently high level within the network.
Food and transport safety: In addition to conscientious, operationally safe loading, the measures we take to protect your food include temperature monitoring, the use of modern, permanently maintained equipment and regular internal and external audits.
Sustainability: We have launched a large number of resource-saving and CO2-saving measures to bring your food to its destination and/or store it in a more environmentally friendly way. In long-distance transport, the first hydrogen fuel cell trucks and battery-electric trucks are already being used in Switzerland. The use of highly efficient, energy-saving refrigeration systems is reducing energy consumption levels. Increasingly, mainly green electricity is being used or produced in-house via photovoltaic systems.
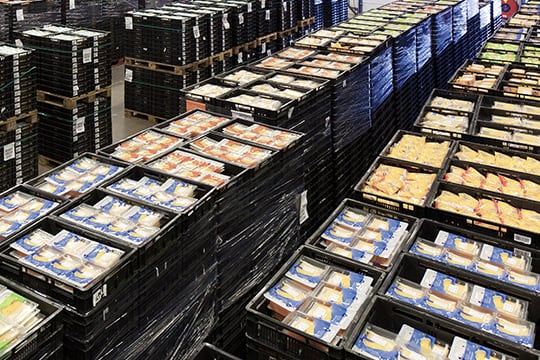